After a decade of stagnated productivity, forecasters predict that the Fourth Industrial Revolution (also known as Industry 4.0) is expected to create incredible increases in revenue for companies and organizations in just a few years' time. However, unfortunately, pilot purgatory can often become a barrier to successful adoption. In overcoming these challenges on being stuck in pilot purgatory, many companies need help to successfully adopt the technologies of the future.
Stuck Pilot Purgatory Use Case
This is one of the best examples of pilot purgatory that I have had in the past with a manufacturing company in India; a huge investment by an end user and the involvement of big automation companies for doing an Industrial Internet of Things (IIoT) project. The project required lots of manpower, wiring and cabling activities in the field with programmable logic controllers (PLCs), and field instruments. Using big data inputs, software, licenses, OPC licenses, etc., but data accuracy was still less than 50% and ultimately not useful for our production and management people. Just making nice looking dashboards was not going to help the plant.
This is not new. Lots of plants in India are going through this same situation; investing money in IIoT and then later not knowing what to do.
A Potential Fix
One of my goals as a professional is to transform the world of manufacturing by creating the easiest and most effective tools for improving manufacturing productivity with reduced losses, cycle time and process optimization, cloud-based analytics, and automated reports to save time and money. Our IIoT can track real-time machine cycle times, losses, overall equipment effectiveness (OEE), productivity, key performance indicators (KPIs), and gives various analytics and reports.
Our solution is not like any traditional, expensive, and lengthy way of doing IIoT as is sometimes done by other automation companies. Here we use different tactics. The table below shows a summary of IoT improvements based on my IIoT experience in the last few years (click for high-res version).
Comparison/Improvement Chart (click for high-res version)
Why We Prefer Cycle Input from Sensors Only
Projects in IIoT require a lot of data from the shop floor (ie, OT). Nowadays, most IIoT projects are driven more from the software/IT side. For them, understanding shop floor technology is quite hard since it’s not very accessible due to multiple PLC suppliers. Original equipment manufacturers (OEMs) are involved and do not want to touch their control panel or do anything in the PLC programming section. They keep all their PLC passwords protected and never want to share with anyone, even their end-user customer. It is tough to cooperate with them during these digital transformation IIoT projects; very few OEM suppliers are supporting. In fact, PLCs are there to control machines or processes, and every change to them can lead to a malfunction.
PLCs play a highly critical role within a factory and thus should not be touched unless there’s a problem with its operation. Most companies understand this and would never allow installing anything that could interfere with PLCs. I also have the same experience when I was an end user in my previous companies. I always prefer that IIoT solutions take input directly from sensors on the production line. Data accuracy is typically 100% when input is taken from sensors compared to input taken from PLCs.
Use Case #1: Manual Assembly Plant in Bangalore, India
With the installation of our IIoT, it had been observed that production efficiency went up just after a few hours.
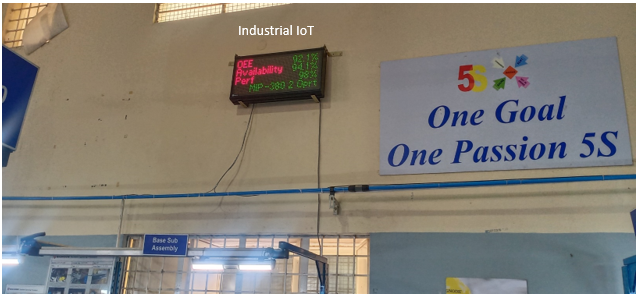
Use Case #2: Pharmaceutical Company in Hyderabad, India
OEE and down reasons were key matrices for them. They had small stop reasons more than 75 and they wanted to record through IoT. Earlier, they used to monitor and record manually, and it was a very stressful and tedious job for the operator. However, with IoT installed, this became very easy.
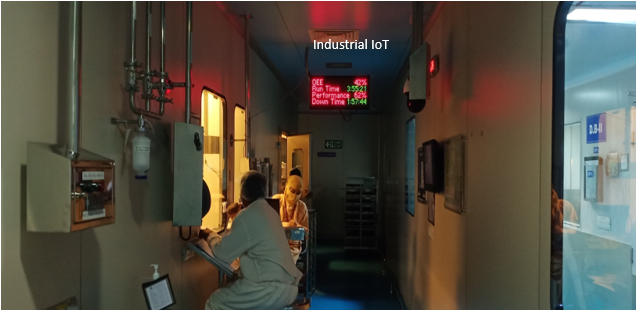
Use Case #3: Distillery Plant in Nepal
One machine had much downtime and a lot of quality rejection. We installed IIoT and it started to track machine downtime and quality reasons, which helped the plant to work on preventive maintenance.