This post was written by Keith Riley and Tim Schrock of Endress+Hauser.
Many temperature applications in the oil and gas, petrochemical, and other industries involve demanding process conditions, hazardous media, elevated corrosion rates, turbulence, vibration, and high pressures and temperatures. In these instances, specialized instrumentation, such as multipoint thermometers, skin-point thermometers, or high-temperature/harsh-environment devices, are available to make the required measurements.
For temperature profiling, multipoint thermometers allow you to measure multiple locations, either horizontally or vertically, within the process. An example of horizontal measurement is reading multiple temperature points at some level in a batch reactor or process vessel. A typical vertical temperature profile would be top to bottom measurements in a tank. These types of instruments are typically referred to as rigid or inline multipoint temperature units. A long thermowell can have thermocouples positioned at various points in the thermowell (figure 1).
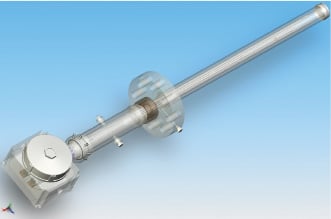
Most of these rigid multipoint temperature assemblies have thermowells that are four-to-six feet long, but specialized thermowells have been assembled that are more than 100 feet long, with up to 40 separate temperature sensors.
In other applications, a multipoint temperature assembly can have multiple sensors spread across the process in an octopus-like array, with each sensing device attached to the end of a flexible cable. In both cases (rigid and array), a single multipoint instrument can provide multiple temperature measurements from a single process connection or access point in the system.
Multipoint temperature measurements
In a rigid design thermowell, the unit bolts to the process vessel via a flange. Wiring from the multiple temperature sensors passes through a safety chamber, which prevents process fluids or gases from escaping, and into a junction box. The thermowell is designed so that individual sensors and wiring can be removed and replaced at the flange (figure 2) without removing the thermowell. The sensing elements are encased in a guiding tube that remains in the thermowell. This allows a faulty insert to be easily exchanged for a new one, thus minimizing maintenance and increasing productivity.
Rigid multipoint thermowells can be mounted across a vessel, vertically from top to bottom, or even at angles (figure 3) to obtain a temperature profile. When mounted horizontally, the thermowell often completely spans the vessel’s width. To prevent damage to the extended thermowell in these situations, a mounting bracket can be installed on the opposite side of the vessel to anchor the thermowell against various forces, such as agitation.
Multiple sensors can be positioned within each thermowell. For example, in a 100-foot-tall reactor, a user could have 10 sensors evenly spaced every 10 feet. For redundancy, the user could also have 20 total sensors, with two thermocouples every 10 feet. If one of the two thermocouples fails, the other would still be able to measure the temperature at that point while the faulty one is replaced.
Theoretically, for a horizontally installed multipoint, the maximum immersion length of each individual multipoint thermometer is the reactor’s internal diameter, as custom assemblies can be made to accommodate various vessels.
Sensors – array style
In an “octopus” array, the sensors are arranged so they spread out across the vessel, much like octopus tentacles. The array is in the upper left corner of figure 4, where it is being used for temperature profiling in a hydrofiner.
In hydrofiners, new environmental standards for low sulfur fuels are driving the need for temperature profiling. These standards and regulations require plants to reduce air pollution emissions, particularly NOX, and are leading to equipment retrofits and upgrades. For example, the sulfur content in mineral oil products must be limited. Typically, this is achieved by catalytic desulfurization in a hydrofiner. Heated to 572°F to 752°F (300°C to 400°C) and raised to a pressure of 362 to 870 psi (2.5 to 6 MPa), the oil is mixed with hydrogen and reacts with the catalyst. The sulfur molecular connection then is converted to H2S and hydrogen carbides.
One of the issues with this process is performing temperature profile monitoring at the different catalyst layers of a hydrofiner. With a limited number of access points available in a hydrofiner, multiple sensors must be inserted at each access point. One way to make multiple measurements from a single access point is to insert a multipoint sensor array. The instrument shown in the top left corner of figure 4 can accommodate multiple sensors as needed based upon the application.
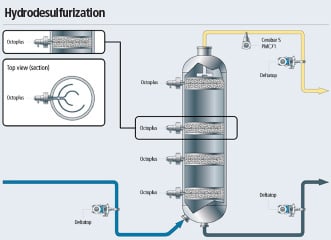
Individual thermocouples are mounted in a single nozzle. The unit’s “tentacles” can be positioned within the reactor as needed to monitor the layer. Using data from multiple sensors, the control and monitoring software can construct a three-dimensional image of the catalyst layer temperatures.
Temperature profiling with a sensor array is also useful in fixed-bed reactors. Due to the solid state of the catalyst, it may not be possible to achieve a homogeneous reaction mixture. Formation of hot spots and cold spots may occur, and coke formation can quickly lead to deactivation of the catalyst.
With multiple measuring points per process connection, sensors can be freely positioned in the reactor to detect problems. As a result, operations can quickly become aware of a degrading process situation and take appropriate action.
Temperature sensors are typically routed directly to multipoint transmitters or to a terminal block assembly that can accept multiple sensors. When transmitters are chosen, each transmitter sends a 4–20 mA signal
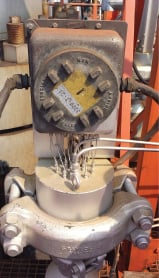
to the control system, one per sensor. The terminal block assembly is used to route the thermocouple cables to the control system’s analog temperature inputs. Either the transmitters or the terminal block assembly is typically housed in an enclosure (figure 5).
Surface temperature measurement
Other groups of applications require temperature measurement, but are not suitable for direct measurement through a sensor or thermowell. This could be due to elevated temperatures, excess fluid velocity in the pipe, corrosion concerns, or the inability to shut down the process should replacement be necessary. Typical examples are steam methane reformers, direct fired heaters, and reactors.
These applications commonly employ an indirect measurement in the form of surface temperature measurement using skin-point thermometers. Another form of indirect measurement is infrared. In many applications, pipes can become “white hot.” An infrared measurement needs a black body to measure temperature correctly. For a skin-point thermometer, the radiated heat or light has very little effect on the temperature measurement.
As with multipoint temperature measurement, the uniqueness of surface temperature measurement is the method of installation, not the measurement itself. Relatively standard thermocouples or resistance temperature detectors are used to do just what the name implies, measure the surface temperature of the pipe or vessel. It is how the temperature probes are secured to the surface that makes them an engineered solution. There are three basic methods to install surface temperature sensors (figure 6):
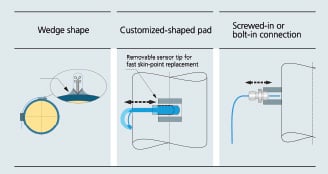
- Wedge shape: The temperature probe is permanently affixed to the tube surface by welding. This provides a fast response time, but the probe will not be easily replaceable if it is damaged or worn.
- Customized-shaped pad: The pad, typically with a radius shape to match the pipe diameter, is secured to the pipe, but the temperature probe is not. The probe is placed inside the pad to ensure consistent contact. This installation method allows for simple and fast replacement of the temperature probe with no need for any cutting or welding.
- Screwed-in or bolt-in: Very similar to the customized-shaped pad version, this method makes it quick and easy to replace the temperature probe. This method is best suited for light duty applications or for those applications requiring a more mechanical means to maintain the probe’s position.
One of the more unique or customized installations happens when the temperature probe’s terminal strip or transmitter cannot be located in the same vicinity as the actual pipe or vessel due to environmental conditions. This normally occurs with furnace pipes. In this case, it is necessary to consider the different thermal displacements that can occur between the zone where the probe terminates and the actual surface of the pipe or vessel. There must be a degree of flexibility or movement, but continuous contact with the surface of the pipe or vessel must be maintained. In these instances, expansion coils can be designed into the temperature probe, or the assembly can be spring loaded (figure 7).
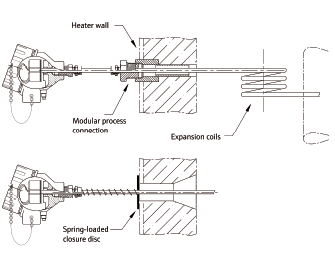
This feature also helps with the integrity of the weld on the pipe. If a rigid thermowell connects the process connection to the weld pad, then expansion and contraction due to thermal effects will be an issue. As the pipe being measured heats and cools, it expands and contracts. If an expansion coil or spring is not used, this adds extra stress to the welds, and they will eventually fracture.
High temperatures and harsh environments
Applications such as gasifiers, Claus units, or steam reformers often have high process temperatures (up to 2900°F), and thus require special high-temperature thermowells and thermocouple temperature probes. Depending upon the application, there are a number of metallic and nonmetallic choices available for the thermowell. Ceramic (nonmetallic) thermowells and protection sheaths (figure 8) are extremely resistant to high temperatures greater than 2900°F (1600°C) and offer very good protection from abrasion. However, ceramic is also brittle and possesses less mechanical load strength than most metals.
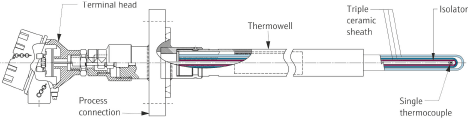
Typical industries or applications where ceramic thermowells are employed include steel, cement, brick kilns, and ceramic and glass production. Ceramic thermowells can also add a layer of protection against gases because they are not porous. They are thus highly resistant to letting gases pass through and damage the internal metallic thermowell (in the case of a ceramic protection sheath) or temperature sensor.
Metallic thermowells provide better mechanical strength than ceramic does, but have lower temperature and abrasion resistance. Examples of some of the exotic metal compounds that can be employed are:
- Inconel 601 – 2147°F (1175°C)
- Incoloy 800HT – 2012°F (1100°C)
- Hastelloy X – 2102°F (1150°C)
Metal thermowells are often used in cement plants, steel treatment, waste incineration, and industrial furnaces.
After long-term use in demanding process conditions with high corrosion rates, pressures, and temperatures—combined with a series of known and unpredictable process phenomenon such as turbulence and highly exothermic local chemical reactions—a crack in the thermowell wall might occur. This can allow the process media to fill the internal volume of the thermowell. In such a case, additional barriers built into the thermowell can contain the process media.
Environmental regulations and the need for better control of processes are driving increased use of temperature profiling in many industries. Temperature profiling involving multiple sensors is used when a single temperature sensor cannot provide the information needed. Temperature profiling is made possible with multipoint temperature sensors that can extend across a vessel or reactor, in either straight or octopus-like configurations. Sensors can also be surface mounted.
For other difficult temperature measurement applications, various specialized sensors and solutions are available. To deal with all difficult sensing problems, it is best to consult with an instrument company that has experience in your specific application.
About the AuthorsKeith Riley has been a product business manager with Endress+Hauser since April 2008. Before this, he was a product manager and regional sales manager with L.J. Star Incorporated, as well as a product manager for Penberthy (Tyco Valves). Overall, he has more than 20 years of sales, marketing, and instrumentation experience in the process industries.
Tim Schrock, area manager for the Endress+Hauser temperature production center, has more than five years of experience in the instrumentation field. He started his career at Endress+Hauser and has held various roles such as technical support engineer, inside sales engineer, and outside sales representative. In his current role, he works closely with the sales centers in the U.S., Canada, Mexico, Brazil, and Chile on temperature applications, while also providing commercial and marketing support.
A version of this article also was published at InTech magazine.