This is an excerpt from the September/October 2012 InTech feature by Fabio Terezinho. For the entire article, please see the link at the bottom of this post.
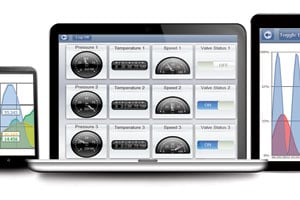
Human Machine Interface (HMI) has evolved significantly from the days in which operations staff had to sit in front of a single screen to monitor a machine or a process. HMI/SCADA (Supervisory Control and Data Acquisition) applications now not only monitor and help control equipment and processes but also provide a huge range of information regarding machine and plant operations. Since many people consider HMI to be a low-end panel-mounted apparatus, the term SCADA will be used to refer to the more advanced applications discussed in this article.
[There are] various ways in which HMI and SCADA systems provide remote access to users. At the most basic, a panel-mounted HMI with built-in web server capabilities provides some limited degree of remote access via a web browser. This access is often only one-way, allowing remote users to view information, but not to make changes.
The next step up is again server-browser access, but this time via local SCADA software, generally running on a PC installed locally at the machine or the process. Although the remote access is still via browser, in most cases, this access is more full-featured than with a simple HMI, allowing remote users to view more information in a wider variety of formats. SCADA server-browser access also usually provides two-way access, allowing for remote adjustments and corrections.
Many SCADA software packages also allow server mobile phone app remote access. As with SCADA server-browser access, remote users have full-featured two-way access. But mobile phone app access can provide other advantages, namely easier and faster loading of the remote application, and faster response to and from the SCADA system.
Modern SCADA systems generally provide server thin-client remote access, allowing any type of PC or other similar device to remotely access the main SCADA system. This type of access is often virtually identical to local SCADA system access, providing a full range of features, albeit at a higher cost than browser or app access. ...
Finally, cloud-based SCADA servers can provide multiple means of remote access at very low cost and are an ideal fit in many applications. This article will discuss all of these remote access methods in detail, focusing on more advanced SCADA-based remote access solutions.
The move to PC-based systems
Whether it is a plant manager checking the latest Overall Equipment Effectiveness (OEE) performance or an operator reacting swiftly to an alarm, the ability to access data quickly from multiple remote locations makes manufacturers more efficient and flexible. Table 2 lists some of the advantages of remote access, which are well known to most manufacturers and will not be covered in detail in this article.
Over the years, various technical advances have provided the required remote access to enable improved operations. As SCADA systems evolved from simple local HMI functionality and became more advanced, they had to move to open standards and networking protocols to communicate with diverse equipment and systems. This opened access to a wide variety of devices that could remotely access SCADA information from just about anywhere and at any time.
Starting in the 1980s, SCADA systems migrated from proprietary hardware to PCs, generally Windows-based. This offered many advantages in terms of graphics, alarming, and trending that improved control and overall plant performance. Many people remember and are keenly aware of the advantages PC-based SCADA brought to local users, in terms of cost and performance.
However, one often forgets how the move to PC-based systems made possible the changes in SCADA information portability and remote access. The first HMIs were designed only to interact with local human operators, and not with other systems or with remote users.
As SCADA systems began to be integrated with other non-proprietary control systems, they started using Microsoft standards to facilitate connections. SCADA information could then be downloaded easily into programs, such as Microsoft Word and Excel, the types of data representation that appealed to a broader range of users.
As a corollary benefit, remote access was much easier to implement with these PC-based Windows SCADA systems, particularly as compared to older SCADA systems based on proprietary hardware and software operating systems.
The introduction of networking standards along with the increasingly open SCADA architectures have enabled this and other types of SCADA-based information to be accessed by a growing number of remote devices.
PC-based SCADA systems opened the way to laptops, mobile phones, and other remote appliances that enable operators and managers to view information from anywhere, enabling plants to run more effectively.
For example, when remote SCADA software became available for the Microsoft Windows CE operating system platform, it allowed developers to more easily implement remote access on a wider variety of hardware platforms. Remote SCADA packages optimized for mobile and embedded operating systems were developed to deliver many of the tools and functionality found in a local PC-based SCADA system to a wide variety of smaller capacity remote devices.
SCADA data
Not so long ago, operator interface meant a local HMI for control of a single machine or process. Today, HMI has morphed into full-featured SCADA systems that often serve as an important component of plant automation by collecting and archiving huge amounts of data. This has increased the need for easier and less expensive remote access, as more personnel want and need access to this expanded amount of data.
Operators, engineers, and managers are expected to respond faster to events, even though total staff counts are the same or lower. Fortunately, remote access tools are enabling greater efficiency, allowing personnel to operate more effectively over a wider geographical area.
For example, a recent expansion of SCADA system functionality has been to include more enterprise data, such as OEE dashboards that present Key Performance Indicator (KPI) data. This type of data has a great appeal to plant managers and executives.
By studying a plant's KPIs with respect to factors such as throughput, quality, and availability, plant managers can remotely determine the machines or parts of the process that need improvement. If a machine's throughput is at 100% with acceptable quality of finished parts at only 80%, a plant manager knows that improvements can be made.
Browsers versus apps
Since operators, engineers, and managers must monitor more processes in more places, they need the ability to access SCADA information from mobile devices. In response to those needs, SCADA suppliers have designed their products to provide a wide range of remote access methods.
Now, authorized users can remotely access data using a variety of devices including PCs, iPads, tablets, and smartphones. Remote access to SCADA systems by mobile devices is typically achieved via a web browser or an app. There is a debate over which method provides better access, but in both cases, the access must be optimized for the smaller screens found on remote devices as compared to PCs.
Users need screens that are correctly sized for their iPhones and Androids, as too much graphical information will slow download speeds, and often result in excess data charges from cell phone providers. Incorrectly sized screens also make remote access cumbersome, as excessive scrolling is often required to view text and graphics information.
Apps are designed specifically for smartphones and other handheld devices, so screens are generally designed correctly. But care must be taken when designing browser-based remote access from SCADA servers, as information must be presented in a format consistent with the hardware limitations of the platform.
Since the programming languages used for iPhones and Androids are different, apps and browser-based applications typically had to be written by SCADA suppliers separately for different devices. This meant users often had to wait months for their smartphone application to be developed or upgraded.
However, many SCADA suppliers are now developing their remote access applications in HTML5, taking advantage of this open standard to develop a multitude of web applications for multiple types of devices at the same time.
Thin clients overcome the issues involved with designing remote access for smartphones and other similar devices, as the thin client is generally a PC or a related device with a relatively large screen size, and with accompanying supporting hardware.
But thin clients are more expensive to deploy, as the hardware costs more up front, and as connectivity generally must be provided by means other than existing cell phone networks. In addition, some SCADA suppliers charge for each thin-client software license, while most provide virtually unlimited smartphone browser or app access at little or no extra cost.
From the web to the cloud
One of the latest developments in remote access is hosting the SCADA system in a cloud-based environment. This enables users to significantly reduce costs and achieve greater reliability, while gaining the ability to remotely access data from a wide variety of hardware platforms over many types of networks ranging from hard-wired to cellular.
In addition to eliminating the expenses and problems related to the hardware layer of IT infrastructure, cloud-based SCADA enables users to view data on devices like smart phones and tablet computers, as well as through SMS text messages and e-mail.
Cloud computing is utilized by SCADA applications in two ways: 1) the SCADA application is running on-site, directly connected to the control network and delivering information to the cloud where it can be stored and disseminated; 2) the SCADA application is running entirely in the cloud and remotely connected to the control network.
Most cloud-based SCADA systems use the first method. The automation functions of the SCADA application are entirely isolated to the control network, with no interface to the cloud. However, the SCADA system is connected to a service in the cloud that provides visualization, reporting, and access to remote users. These applications are commonly implemented using public cloud infrastructures.
With cloud-based SCADA, all of the computing power, storage, and redundancy required for remote access are provided by the cloud providers' servers. This makes every user a remote user, with no additional effort required by the end user after establishing a connection from the local SCADA system to the cloud. It also reduces deployment time from weeks or months to a few days, or even a few hours.
Since the IT layer is removed from the plant, all updates, security measures, and patches are performed instantaneously across the system without any input required from the end user. System availability for remote users is improved because the cloud provider usually offers multiple, redundant Internet and other connections, whereas most traditional SCADA environments generally depend on a single Internet provider.
Cloud-based computing also poses some new security challenges, as the data in the cloud is generally stored in a shared environment. Users must trust the long-term stability and the security measures of the cloud provider, and must be confident that they can take control and ownership of their data if the provider is not performing to expectations.
With respect to security, it is important to remember reputable cloud providers are aware of the new security challenges and have entire departments devoted to learning about the latest possible threats and implementing necessary precautions. There is also reason to believe that existing Internet law on the ownership of data will be extended to protect cloud users.
Whether remotely obtaining information using networking protocols, enabling more authorized users to access the SCADA system from their smartphone, or even moving their SCADA IT infrastructure to the cloud, more and more manufacturers are benefiting from the remote-access capabilities of their SCADA solutions.
In the majority of cases, remote access has increased flexibility, improved overall efficiency, and reduced operating costs. Less staff is required to operate plants; plant managers can make informed decisions to improve productivity; and workers do not need to drive to distant locations to retrieve data.
Not all manufacturers are ready to move to cloud-based SCADA, but most have benefited from the move to advanced SCADA solutions that have ushered in the era of access to data anytime from anywhere via a wide variety of platforms.