Radiometric or gamma level/density instruments are most often used in applications where other measuring techniques fail due to extreme temperatures or pressures, toxic media, complex geometries of vessels or pipes with difficult installation requirements, high viscosities, changing fluid behaviors, or abrasive or corrosive properties of the process media.
Because a radiometric measuring system is a noninvasive measuring technique (i.e., the emitter and detector are mounted external to the process), the behavior of a medium inside a vessel can be precisely observed with equipment fitted outside the vessel (figure 1).
A very simple installation is shown in figure 1. Because there is an agitator inside the vessel, installing a level measuring device inside the tank, such as an ultrasonic or guided radar instrument, may not be suitable. Depending on the conditions inside the vessel, the medium may vaporize, or the rotating agitator might cause a vortex at the surface of the fluid. These conditions may interfere with other types of level measuring devices, which are installed inside the vessel walls. With radiometric measurement, it is possible to detect all medium conditions.
Benefits of using radiometric include:
- noncontact and noninvasive measuring
- guaranteed process safety due to being outside the process vessel
- precise and repeatable measurement for level, density, and interface applications
- safe and easy to install
- reliable measuring equipment
Radioactivity basics
Radioactivity can be roughly classified into three types, each emitted by the decay of the radioactive isotope:
- alpha radiation: particle radiation in the form of a helium nucleon (alpha particle)
- beta radiation: elemental particle radiation in the form of electrons and/or positrons (beta particle)
- gamma radiation: high-energy electromagnetic waves similar to radio waves and light
With radiometric level and density measurement, only gamma radiation is used. Alpha and beta radiation are not strong enough to penetrate solid material, but the high energy and high-frequency wavelength of gamma waves radiate through material in the beam's path. When a gamma ray passes through matter, the absorption rate is proportional to the thickness of the layer, the density of the material, the absorption cross section of the material, and the energy of the wave.
Thus, absorption and energy are the main factors that influence the size of the required source and the quality of radiometric measurement. Typical industrial isotopes used in radiometric applications are cesium-137 (Cs-137) and cobalt-60 (Co-60). The two isotopes differ in their physical attributes, with cesium having a longer half-life but lower emitted gamma radiation energy. Cobalt-60 has a shorter half-life with higher energy.
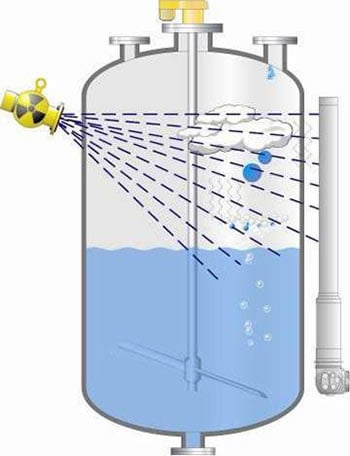
Half-life is the length of time that it takes for the source to decay until it reaches half of the activity generated by the original isotope. The half-life of Cs-137 is 30.17 years, and Co-60 is 5.2 years. Typically, Cs-137 is used in industrial applications, because it requires less maintenance (i.e., replacing the sources) and its activities or strength are sufficient for most applications. In special cases, Co-60 might be required for radiating through thick material or high-density fluids. A formula determines the source size, taking into account anything in the beam path (vessel walls, insulation, heating coils, and obstructions) and the distance from the source to the detector.
The calculation uses the following equation:
P = Fa · Fs · Fi
_________________
K
where:
P = the required source activity in mCi
K = the isotope coefficient (K = 3.55 for Cs-137 and 13.2 for Co-60)
Fa = r2, where r refers to the distance from the source to the detector
Fs = absorption, depending on the density of the material and the thickness of the material in the beam path
Fi = the sensitivity of the detector
Today, such calculations are done in a software program, which takes all the guesswork out of the sizing (figure 2). Most manufacturers have a sizing program. The program can calculate the size of the source and the exposure rate at the source holder and the detector-and use these calculations to estimate the accuracy of the application. All sizing is based on "as low as reasonably achievable" (ALARA) guidelines. That is, the size of the source is limited to the smallest size required to make the required measurement.
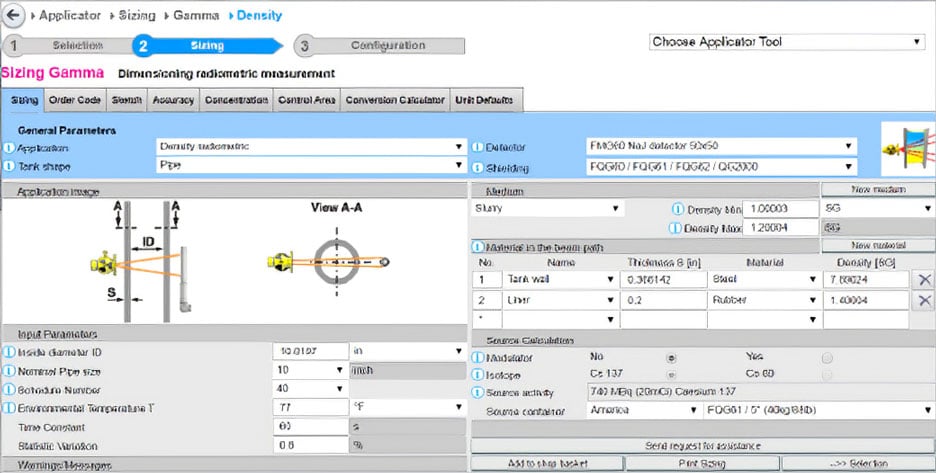
Gamma elements
The typical gamma level or density system consists of four parts: the radioactive source, a source holder, a detector, and the brackets to mount the components to the process vessel or pipeline. The function of the source holder (figure 3) is simply to hold the radioactive source in a safe manner. The source holder is a lead container with a slot cut to direct the gamma wave toward the process. The emission angle through the slot will normally be about 6 degrees wide and 5, 20, or 40 degrees tall. This means radiation levels are very low at the source holder unless someone is directly in the beam path.
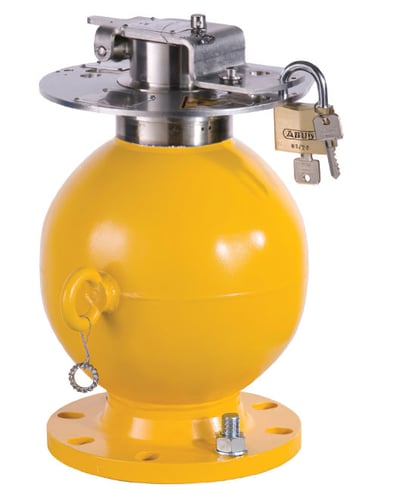
Although not recommended, a person would have to sit on a source holder for two and a half hours to receive the same radiation dose as flying from New York to Miami in an airplane. The beam path must be shielded or screened to prevent someone from accidentally getting a finger or hand in this beam path. Per Nuclear Regulatory Commission guidelines, the source holder must have a lockable shutter mechanism to block the radiation, or a mechanism to rotate the source away from the opening. This renders the source holder safe, allowing maintenance personnel to perform work inside the vessel and to install or remove the source holder. Detectors (figure 4) have changed much over the past few years and have become much more sensitive and responsive.
The purpose of the detector is to detect and quantify the amount of radiation received. In older gamma systems, an ion chamber was typically used in density applications. Modern detectors use a scintillator tube sensor. The scintillator tube absorbs the gamma photon and converts it into a light pulse. These light pulses create a photoelectron at the photo cathode, where they are multiplied and converted to an electrical pulse. These pulses or counts determine how much radiation is being received by the detector. With a scintillation detector tube made of sodium iodide (NaI) crystal or PVT plastic, the energy required to make an accurate measurement is minimal. For example, an 18-inch slurry pipeline might need a 250-mCi Cs-137 source to have enough activity for the older type of ion detector to work.
With a scintillation tube detector, a 30-mCi Cs-137 source handles the same application. Reduced radiation ensures the safety of people working in the area, and the detectors are much more stable even with large temperature changes. Flexible scintillation detectors offer easy installation but may not be as sensitive as rigid scintillators. In a density application, the higher the count rates, the lower the density. In a level application, the same applies, the higher the count rate, the lower the level in the process vessel. The detector contains a transmitter that converts the count rate to a 4-20 mA HART output signal to be sent to the control or monitoring system.
Profibus PA or FOUNDATION Fieldbus outputs may also be available. With today's more sensitive scintillator detectors, it is often possible to extend the life of a gamma system. Old-style detectors require so much more energy, they tend to not work reliably as the source nears its half-life. A scintillator-style detector extends the life of the source, eliminating the need to purchase a new source and the cost of disposing the old source. As discussed, radioactive sources decay at a specific rate. In older gamma systems, frequent calibration was required to compensate for the decreased source activity.
Today's detectors have built-in source decay compensation. They automatically compensate for decay, reducing calibration requirements and maintenance costs. Some detectors use a Geiger-Mueller tube for radiation detection. These units are not as sensitive as scintillator tube detectors, but they work well for point level detection and cost less.
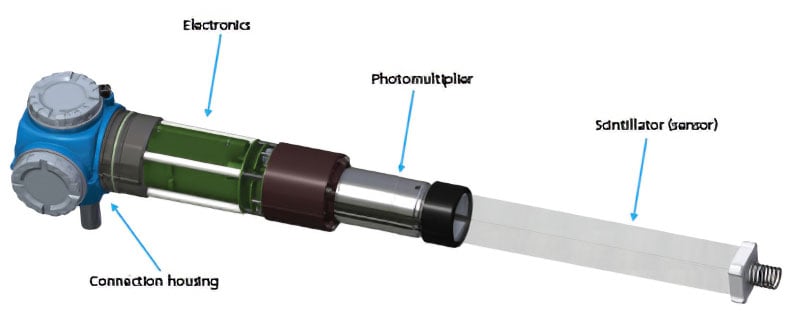
Outside interference
Radiation from external sources can be a major problem for gamma-based systems. External radiation can come from radioactive material in the process media, other gamma-emitting devices, or radiography testing. Refineries, petrochemical plants, and heavy chemical plants may do routine radiography testing of pipelines and vessels to ensure their integrity. Every time technicians perform an x-ray of a pipe or vessel, there is a huge surge in the background radiation.
The output from a gamma-based detector in the plant will most likely be affected. The increase in the background radiation is picked up by the gamma detector, causing the transmitter to report a much lower level than is actually present. This can cause major upsets in the process and may pose a safety risk.
In the past, plants would try to shield the gamma detectors or put the control loop in manual during radiography testing to avoid process upsets. Today, a gamma modulator can eliminate any issue from external radiation.
A gamma modulator is mounted between the source holder and the process. It consists of two absorber rods rotating at a fixed speed directly in the gamma beam path. When the absorber rods are in line with the gamma beam, they attenuate the gamma energy so no energy reaches the detector, and the gamma detector reads the background radiation. As the absorber rods rotate parallel to the gamma beam path, the gamma rays pass between the absorber rods and continue to the process vessel and the detector.
The detector is configured to look for this modulated gamma energy. Internally, it subtracts the background radiation reading when the modulator is in the open position (figure 5). The resultant value is thus not affected by background radiation.
Modern gamma systems for level or density measurement are reliable, accurate, and safe-and often work in level and density applications where other solutions will not. End users do need to make sure their supplier is knowledgeable about gamma licensing requirements and can provide full gamma support for your facility.
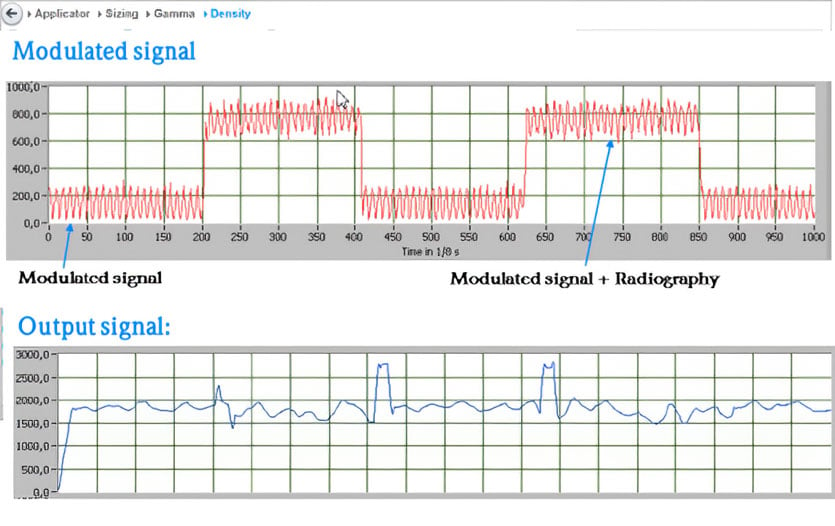
A version of this article also was published at InTech magazine.