This post was written by Wally Baker is a global pressure content marketing manager with Emerson Automation Solutions.
Accurately measuring liquid, gas, and steam pressure is a basic requirement for many industrial processes to operate safely, efficiently, and with optimum quality control. In addition to directly measuring pressure values, pressure measurements can be used to determine or infer flow rates, fluid levels, product density, and other parameters. As a result, many plants rely on pressure-measurement devices to get required field measurements.
Some example applications using pressure or differential measurements are:
- flow rate through a pipe
- level of fluid in a tank
- density of a substance
- interface between two or more liquids in a tank
For example, if a constriction, such as an orifice plate, is placed in a pipe, pressure will drop in a predictable way. By measuring the pressure in the pipe both before and after the orifice plate, the rate of flow through the pipe can be calculated.
This article examines the elements of pressure measurement and looks at some recent advances in the technology for better pressure measurements.
Absolute, gauge, and differential pressure
Pressure-measurement devices can be categorized according to the measured reference pressure. The three reference pressures are:
- Absolute: Absolute pressure measurements compare measured pressure to a perfect vacuum (0 pounds per square inch, absolute [psia]).
- Gauge: Gauge pressure measurements compare measured pressure to the pressure of the surrounding atmosphere (approximately 14.7 psia) as a reference pressure. Changes in atmospheric pressure (such as those due to changes in the weather) are taken into account for the output of a gauge transmitter. Gauge devices are often used to measure level in holding tanks that are open to the atmosphere.
- Differential: A differential pressure measurement uses a second process pressure as a reference pressure. Differential pressure measurements are often used to infer the rate of flow through a pipe by determining the pressure drop that occurs from one point in a system to another, such as the drop that occurs across an orifice plate in a pipe.
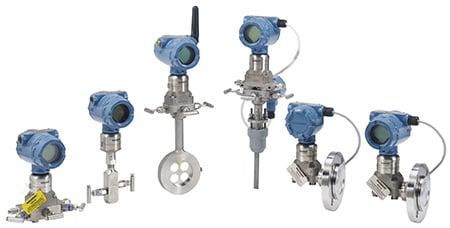
Modern transmitter basics
Pressure sensors and transmitters have been used in the process industry for decades, starting in the 1940s with pneumatic transmitters that supplied a pressure signal to pneumatic controllers. In the 1950s, electronic transmitters appeared, which converted the pressure signal to a 4–20 mA signal that could be used by electronic controllers and, later, by computers. HART was added to the 4–20 mA signal in the 1980s, creating the smart pressure transmitter. Fieldbus digital signals came later, and now wireless is available in both types of smart transmitters.
Smart transmitters allow more than just the pressure value to be reported from the field. Now a significant amount of information can be reported from a single pressure transmitter. One of the most important advances of smart transmitters is in the area of diagnostics.
Most smart pressure transmitters include a basic set of diagnostics that notifies the operator when the device is broken or needs to be serviced. Today’s more advanced smart transmitters provide additional diagnostic insights not only into the state of the transmitter, but also into the electrical loop and process itself, issuing proactive alerts so operators can respond immediately and avoid downtime. New advances in diagnostics include:
- Process monitoring: Pressure transmitters can listen to the background noise of a process and detect deviations from normal operation that could signify plugged impulse lines or more serious issues with the process itself, such as distillation column flooding, flame instability, or pump cavitation.
- Loop monitoring: Diagnostics can monitor the integrity of the electrical loop that connects a field device to the control room to notify operators of any irregularities such as water in housings and junction boxes, wire corrosion, or unstable power supplies.

Going wireless
Traditional wired pressure transmitters require a supporting infrastructure including wire, cabling, conduit, junction boxes, marshalling cabinets, and I/O to transmit the pressure signal back to the control system. This infrastructure sometimes makes it too difficult or expensive to install pressure transmitters in certain locations.
Installing and implementing wireless devices can take up to 75 percent less time than traditional wired devices with the elimination of wiring and construction labor, and the capital costs associated with wireless technology can be up to 40 percent less. In addition, the insights gained from added pressure monitoring points can help extend the life of assets, creating an even greater return on investment. With a battery-powered wireless pressure transmitter, measurements can be made and transmitted anywhere a pressure transmitter can be installed in a pipe, tank, or steam line for flexibility in a variety of applications.
Improved process connections
The way a pressure transmitter is physically connected to the process can greatly affect the overall accuracy and reliability of the measurement. Simple installations often use impulse tubing that is prone to leaking, plugging, freezing, and other issues to connect sensors. More complex applications, including those on tanks and meter runs, can require multiple components, pipe penetrations, and connections that can increase the amount of impulse tubing required.
Newer pressure transmitters are available in compact assemblies that use fewer components, are simpler to install, and require less ongoing maintenance. These solutions permit close coupling, a best-practice installation procedure that results in more accurate measurements.
In traditional differential pressure (dP) flow applications, for example, integrated flowmeter assemblies eliminate a significant amount of impulse tubing. These flowmeters can replace multiple transmitters that formerly required many mechanical parts and multiple pipe penetrations, which contributed to leaking, plugging, freezing, and inaccurate process measurements.
In tank level applications, an electronic dP remote sensor system can even be used to replace impulse tubing with two pressure transmitters installed on the top and bottom of the vessel

and connected electronically. The remote sensors eliminate impulse tubing and associated environmental effects. The system also eliminates the need to heat trace the impulse lines and protect them from freezing.
Heat tracing can add considerable cost and complexity to any process and requires a great deal of maintenance to keep it operational, because applications using heat tracing suffer from frequent failures. These measurement challenges and suboptimal performance can lead to lower throughput, degraded product quality, and cost overruns.
Some dP level transmitters can address these challenges with specialized remote seals to expand the temperature operating range.
The remote seals can operate in hotter or colder temperatures than traditional transmitters can. With this solution, an intermediate diaphragm seal in the transmitter separates two different fill fluids with different optimal operating temperatures.
For example, on a high-temperature application, the high-temperature fill fluid is only used immediately next to the hot process, and a traditional fill fluid is used for the remainder of the

connected capillary. The solution is not dependent on heat tracing and produces more reliable, accurate, and faster process measurements, particularly in extreme conditions.
Liquid versus gas pressure
The factors that influence the pressure of a liquid are different from the factors that influence the pressure of a gas. When measuring pressure, it is important to understand the pressure properties of liquids and gases. The hydrostatic pressure exerted by a liquid is influenced by three factors:
- height of liquid in a column
- density of the liquid
- pressure on the surface of the liquid (vapor space)
The pressure at the bottom of a column of liquid increases as the height of the liquid in the column increases. Pressure is affected by the height rather than the volume of a liquid.
Unlike a liquid, a gas exerts equal pressure on all parts of the container in which it is held. Two factors affect the pressure exerted by a gas:

- volume of the container in which the gas is held
- temperature of the gas
The relationship between pressure, temperature, and volume of a gas can be determined by applying the ideal gas law.
Ideal gas law: PV = nRT
Gas pressure is affected by changes in temperature. If the volume of the vessel holding a gas and the amount of gas are unchanged, the pressure exerted by the gas on the vessel walls will change in proportion to changes in the temperature of the gas. Or simply stated, by measuring the pressure and temperature in the tank, you can measure the gas.
Measuring flow
A common use of a pressure measurement is to infer a fluid’s flow rate through a pipe. As a fluid flows through a pipe restriction, the fluid pressure drops. The pressure of the fluid flowing through a pipe is greater on the upstream side of the restriction and lower on the downstream side.

If pressure is measured before and after the restriction in the pipe (e.g., a flow element such as an orifice plate, venturi tube, flow nozzle, wedge, or annubar), the square root of the pressure drop is proportional to the flow rate of the fluid through the pipe.
Measuring level
The level of a liquid in a tank or vessel can be determined from a pressure measurement by this equation:
height = pressure/liquids specific gravity
Closed tanks or vessels need a dP transmitter to account for the vapor space pressure. Open tanks or vessels need an absolute pressure transmitter or a dP transmitter with the low-pressure side vented to the atmosphere.
Measuring density
Pressure is equal to the height of the column of liquid being measured multiplied by the specific gravity of the liquid. Therefore, if the height of the column is a known constant, as in the case of the distance between two pressure-measurement points on a vessel, the density can be inferred from the pressure reading using the following equation:

specific gravity = pressure/height of liquid (level)
Specific gravity values can then be converted to density or mass-per-unit-of-volume units such as grams per cubic centimeter. Density measurements are often used in the brewing industry to determine stages of fermentation.
Even after decades of use in industrial applications, pressure measurement technologies continue to advance. These advancements make traditional measurements easier, and often allow measurements in areas where they were not possible before.
About the AuthorWally Baker is a global pressure content marketing manager with Emerson Automation Solutions. He manages Rosemount's pressure product launches and works with users on how to better understand their pressure uses and product needs. He has been in the process control industry since 1999 in various roles, including pressure engineering, temperature global marketing, Singapore wireless marketing, and oil and gas business development.ciation.
A version of this article also was published at InTech magazine.